Thermal-mass gas metering: Proven for years, certified for the future
By Konrad Domanski, Product Manager Gas Flow Systems, Sensirion
Thermal-mass technology is a proven means for measuring the flow of gasses and liquids. Technological advances and miniaturization have enabled the use of the technology for high-volume, cost-sensitive applications such as natural gas metering.
Two recent studies now also confirm the long-term reliability of this technology for applications in harsh environments. The studies investigated thermal-mass gas meters following operation in the field for up to over 10 years. They concluded that all meters were operating well within the accuracy limits prescribed during service and that the majority of meters still fulfilled the requirements for brand-new gas meters.
Coupled with the release of a dedicated European standard in 2021 (EN 17526), thermal gas technology is therefore a cost-effective, proven and reliable solution for gas metering that is already powering millions of gas meters worldwide. Additionally, it offers extensive self- and network-diagnostic capabilities and is ready for a wide range of natural gas compositions including hydrogen blends and pure hydrogen.
Thermal-mass measurement principle
For the past 80 years, thermal-mass technology has been used for measuring flow in the most critical applications such as life-sustaining medical ventilation, air intake regulation in car combustion engines, building ventilation systems and control of sensitive industrial processes. The thermal-mass measurement principle is the most versatile and robust way to measure flow. Until recently, however, it was prohibitively expensive for high-volume, price-sensitive applications.
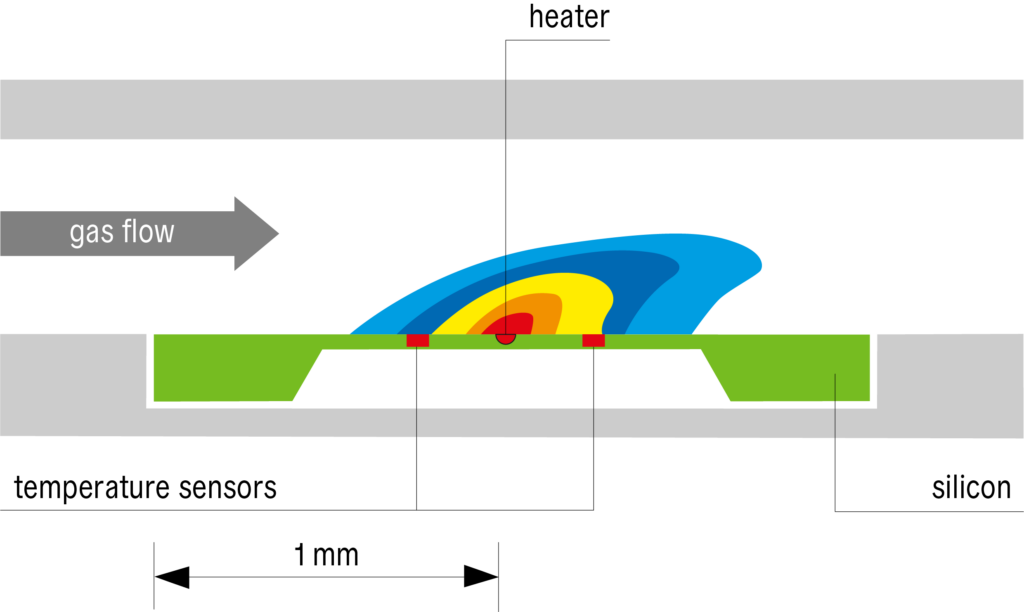
Figure 1: Thermal-mass measurement principle. A heater and two temperature sensors can be integrated on a single silicon chip. The flowing gas alters the heat distribution profile around the heater. The temperature difference detected by the two temperature sensors is proportional to the amount of gas flowing.
With the progress of MEMS (micro-electromechanical system) technology, the thermal-mass flow measurement principle has been realized on a single silicon chip. Highly integrated CMOS processing of such chips allows for effective miniaturization and high-volume production. With these advances, the cost of thermal-mass technology has been radically reduced to the point where it is an attractive solution not only for high-end applications but also for low-cost, high-volume devices such as disposable flow sensors and gas meters.
Thermal-mass technology for gas metering
The application of thermal-mass technology in gas metering was pioneered by Sensirion in the early 2000s. The main benefits of this implementation are excellent accuracy, compact size, ultra-low power consumption (critical for battery-powered gas meters) and, above all, a very attractive cost. The latter is made possible by the integration of the flow sensor, signal processing and analysis electronics, and calibration data storage in a single semiconductor chip. Apart from the flow, thermal-mass sensors can also readily measure various thermal properties of the gas to compensate for variations in gas composition. This makes thermal-mass gas meters an ideal choice for measuring consumption of natural gases with a very wide composition range as well as for gas blends with hydrogen or even pure hydrogen.
The first thermal-mass gas meters were installed in the field in 2007. Following an initially slow adoption of the technology, the rollout has significantly accelerated in recent years and to date over 6 million gas meters worldwide rely on this proven way to measure gas flow. Additionally, 33 million cars and 45 million medical devices rely on Sensirion’s thermal-mass flow sensors. The main factor that initially limited the adoption of the technology for gas metering was the perceived lack of a track record in the field. Even though thermal-mass technology had been proven over the years in many other applications, it was a relative newcomer to the gas metering industry – an industry that values robust performance, safety and reliability above all else.
Various national and international standards regulate the required accuracy of gas meters. Different accuracy classes exist, with class 1.5 being the most widely used worldwide. OIML R137 and EN 17526 (the dedicated thermal-mass gas metering standard being published in 2021) define the maximum permissible error (MPE) for temperature-compensated class 1.5 gas meters (such as thermal-mass meters) as 2% and 3.5% at high and low flow regimes, respectively. OIML R137 additionally prescribes 2x MPE (3.5% / 6.5%) for meters that have been re-measured following in-field service. Hence, the 2x MPE is widely accepted as the bar that a meter has to clear while in service (typically 10–15 years).
Field studies of reliability of thermal-mass gas meters
By 2021, a significant number of thermal-mass gas meters had already been operating in the field for over a decade. Two independent studies recently looked at how different types of thermal-mass meters perform after having been operated in gas for up to over 10 years.
The first study, conducted by NMi – a Dutch notified body – looked at industrial G10, G16 and G25 meters manufactured by MeteRSit and installed in Italy between 2013 and 2016. The institute randomly selected 20 meters from a list of the 2,749 available. These were later collected by the manufacturer (19 meters – one was installed in an inaccessible location) and sent to NMi for read-back measurement. The said measurement involved measuring each meter both in air and natural gas between Qmin and Qmax flow rates. It was found that all meters, regardless of the number of years in service and accumulated measured gas volume, were still well within the 2x MPE allowed. Additionally, all meters performed within 1x MPE in gas, and 15 of the 19 meters also in air. That is to say, most of the meters performed as well as brand-new devices.
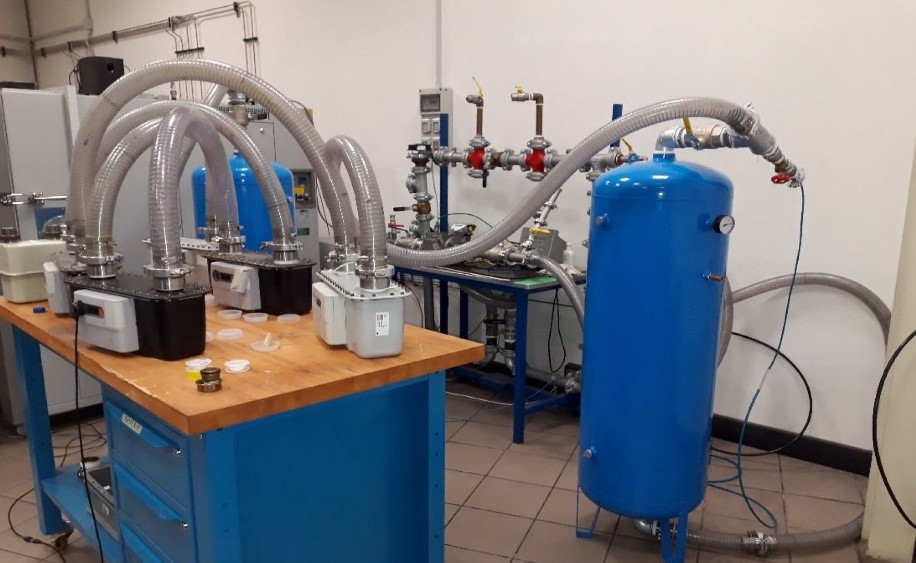
Figure 2: Test setup used by NMi to investigate field-returned
industrial meters manufactured by MeteRSit.
The second study involved 35 “EGZ” G4 residential meters that were built by ABB and installed in Switzerland between 2010 and 2011. These meters were operated for 9 to 10 years before being removed from the field and remeasured. The study was performed by MEMS AG, whose measurement infrastructure was certified by the Swiss Federal Institute of Metrology, METAS, in preparation for the investigation. Again, the authors measured all meters between Qmin and Qmax flow rates both in air and natural gas. Similar to the study conducted by NMi, all meters measured performed well within 2x MPE in both air and gas. Additionally, all 35 meters were still within 1x MPE when tested in gas, and 31 of the 35 also in air.
Figure 3: Flow errors measured in a) natural gas and b) air for 35 EGZ G4 meters between Qmin and Qmax. The blue and red broken lines represent the maximum permissible errors as defined by OIML R137: 1x MPE for new meters (blue) and 2x MPE for field-return meters (red). The black broken line represents the average of the 35 measurements.
Of the 35 meters measured, 3 were installed in a pressure reduction station and experienced unusually high flow rates. In fact, they accumulated measured volumes approximately 14 times higher than the other 32 meters (280 000 m3 vs 20 200 m3 over 10 years). It would take an average meter 140 years of operation to accumulate such an amount of gas measured. Importantly, all 3 meters were still within 1x MPE for both air and natural gas – a benchmark for new gas meters.
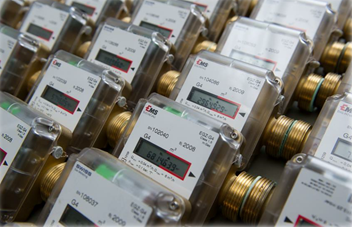
Figure 4: EGZ G4 meters of the type measured in the study conducted by MEMS AG.
What the two studies had in common is that the tested gas meters were based on the key metrological units manufactured by Sensirion AG: CMOSense® gas metering modules. They also both confirmed that thermal-mass gas meters are still as good as new after over 10 years of operation in the field.
Even if the errors were to double over the next 10 years of operation (of which there is no indication), the meters would still be within the 2x MPE allowed by OIML R137. Hence, one can conclude that thermal-mass meters demonstrate the ability to operate reliably in the field for over 20 years. This is significantly longer than the lifetime of a typical gas meter. The metrological unit appears even more stable than that, given that it is unaffected by the very high volume of gas measured (14x the average). It can thus be concluded that it would easily outlive the other parts of the meters.
EN 17526 – new thermal-mass gas metering standard
The maturity of thermal-mass technology for gas metering applications has been recognized by CEN with the publication of a dedicated European standard in 2021. “EN 17526. Gas meters. Thermal-mass flow-meter based gas meter” outlines the requirements and tests needed to bring thermal-mass gas meters into the field. It is a harmonized standard, meaning that it builds on the normative documents previously developed for diaphragm and ultrasonic gas meters. It is also compatible with international norms such as OIML R137. Meter manufacturers used to the existing standards should not find any surprises in the new thermal-mass norm. From now on, the dedicated thermal-mass gas metering standard will remove a significant uncertainty previously associated with certifying such meters because the requirements and test plans are clearly laid out in the dedicated standard. EN 17526 is also the first static measurement principle standard to combine both residential and C&I (up to G25) meter sizes in one document.
Furthermore, that the related norm has been selected as the first one to also cover, upon revision, renewable gases such as hydrogen and biomethane is an important step for thermal-mass technology: it paves the way to harmonizing all other EN gas meter standards and thus supports energy transition initiatives in Europe, including from a normative perspective.
Ready for hydrogen and biomethane
The most important upcoming development in the gas metering industry is the onset of injecting hydrogen into the grid. It is widely expected that this will be a gradual process, with initially up to 30% hydrogen being blended with natural gas before a switch to 100% hydrogen occurs. Thermal-mass gas meters are exceptionally well-suited to measuring both gas blends with hydrogen and pure hydrogen alike. Sensirion’s thermal-mass gas meter modules are already capable of both[1], achieving MID accuracy.
A further advantage is that the meters can retain their compact form factor regardless of the hydrogen content. This is not the case for diaphragm meters, which have to triple in size in order to measure pure hydrogen (due to the three-times lower calorific value of hydrogen compared to natural gas). Furthermore, existing ultrasonic solutions also cannot effectively measure pure hydrogen without increasing in size and employing faster, more costly electronics to compensate for hydrogen’s extremely high speed of sound.
The second upcoming development to support the energy transition is the injection of biomethane into the grid. This renewable gas often comes with a significant CO2 content. Fortunately, Sensirion’s gas metering modules already accurately measure natural gas containing a relatively high fraction CO2, while the company’s thermal-mass technology, which can even measure pure CO2 flow, is currently widely used in medical applications.
Future-proof technology
With the upcoming multiplication of injection points into the grid and an increased hydrogen and biomethane content, the calorific value of the gas will vary significantly more than it currently does – both geographically and temporally. This will have to be matched with either a multiplication of gas chromatographers installed at various critical points in the grid or a switch to direct energy metering. The latter is an especially appealing solution, which would represent a paradigm shift for gas metering. Thermal-mass gas meters measure not only the volumetric flow of gas, but also its various thermal properties. The latter are used to identify the gas in the pipe and to correctly translate the sensor signal to the volume of gas flowing through the meter. Thermal-mass gas meters can already output a hydrogen index of natural gas blends or even provide an indication of the calorific value of the gas. Hence, thermal-mass technology is especially well-suited for future energy content monitoring at meter level.
Figure 5: The gas grid is expected to become more complex with new injection points and renewable gasses blended with natural gas.
Thermal-mass gas metering: Proven for years, certified for the future
Recent developments have brought the cost of thermal-mass technology to the point where it has emerged as a very attractive solution for gas metering applications. Long-term field reliability studies indicate that the lifetime of thermal-mass gas meter modules is significantly longer than the design life of a typical gas meter.
The publication of a dedicated thermal-mass gas metering standard in 2021 recognizes the maturity of the technology and paves the way to more widespread adoption of this well-proven method for flow measurement in the gas metering industry. In addition to attractive cost, reliability and very compact size, thermal-mass technology also offers extensive self- and network-diagnostic capabilities[2] (e.g. air recognition for tampering detection). Finally, the technology can readily cope with measuring natural gas with a very wide composition range, as well as pure hydrogen and natural gas-hydrogen blends of any concentration. Direct energy metering is the next frontier, and it is clear that thermal-mass technology has a significant advantage over current solutions in this area.
Further information:
About Sensirion – Experts for Environmental and Flow Sensor Solutions
Sensirion is one of the world’s leading developers and manufacturers of sensors and sensor solutions that improve efficiency, health, safety, and comfort. Founded in 1998, Sensirion now employs around 1’000 people at its headquarters in Stäfa, Switzerland and in numerous international subsidiaries. Sensirion sensors can be used to measure a wide range of environmental parameters and liquid flow rates precisely and reliably. The company’s aim is to make the world smarter with pioneering sensor technology. As a pioneer in innovation, Sensirion develops solutions for the specific needs of customers and partners from the automotive, industrial, medical technology and consumer electronics markets, as well as high-quality products for cost-efficient mass production. More information and current key figures at www.sensirion.com.
One of the hallmark features of Sensirion products is the use of its patented CMOSens® Technology, which allows for intelligent system integration of the sensor element, logic, calibration data and digital interface on a single chip. Sensirion’s credentials as a reliable supplier are evident from its loyal customer base, reputation for quality (ISO/TS 16949) and excellent customer pedigree.
About the author
Dr. Konrad Domanski is a Product Manager at Sensirion, a Swiss high-tech sensor company. He is responsible for the definition, product lifecycle management and certification of thermal-mass sensor solutions used in smart gas metering products worldwide. Konrad Domanski has broad experience in international project management and holds a PhD in Material Science from the Swiss Federal Institute of Technology in Lausanne (EPFL).
[1] https://www.sensirion.com/en/about-us/newsroom/sensirion-specialist-articles/microthermal-measurement-principle/
[2] http://spintelligentpublishing.com/Digital/Metering-International/issue6-2015/offline/download.pdf