Reliability Centered Maintenance (RCM) – Implementation and Benefits
By Catarina Barros 1 and Miguel Massala 2
- INTRODUCTION
An organization may find it difficult to remain competitive without introducing new management techniques in this non-stop evolving economy. Right now, the world is going through a critical and challenging period triggered by COVID-19, which has forced organizations to make swift day-to-day decisions based on the developments of the pandemic and subsequent global reactions to it. We will use these changes to analyze our maintenance as a whole and clarify what we can improve. The methodology that we will present in this article will be an option that you can follow and implement in a post-quarantine.
RCM is a methodology that is seen as a proactive response to the current competitive market, and one in which companies should keep up to date with.
The implementation of this methodology, which serves to optimize an organization’s maintenance strategies, will boost the company’s productivity and impact its sustainability.
This article seeks to publicize and popularize the RCM methodology, and outline the practical im-plementation process for it, offering surveyed sta-tistical data carried out across several Portuguese and international companies from various sectors.
- WHAT IS RCM?
RCM originated in the aviation industry during the 1960s. During this time, the high costs associated to preventive maintenance, including frequent overhauls or replacements of aircraft compo-nents, spurred a special investigation into the ef-fectiveness and efficiency of these maintenance activities.
In 1974, the United States Department of Defense asked United Airlines to analyze the processes used in the civil aviation industry to develop air-craft maintenance programs.
A pioneering investigation, conducted by Nowlan and Heap of United Airlines, led to the publication of a report in 1978 entitled “Reliability Centered Maintenance”. During this this investigation,
Nowlan and Heap sought to monitor hundreds of mechanical, electrical and structural aircraft com-ponents, having concluded that as the compo-nents aged, it became possible to identify a cer-tain failure pattern.
According to Moubray (1997), RCM is a process used to ensure that any physical asset continues to fulfill its desired functions, in the context of its preferred operational use. Duarte and Fortes (2009) define RCM as a asset management meth-odology used to determine maintenance tasks ca-pable of ensuring that a system or process meets the needs of its users, within the context of its op-erations.
SAE Standards JA1011 / JA1012 define the RCM as a specific process used to identify the policies and strategies that must be implemented to con-trol the causes and modes of functional failures of any asset running its given operations.
The application of this method involves identifying actions that help to reduce the probability of failure for an asset, increasing its reliability and availabil-ity with the overall expectation of lowering the number of failures it will incur, subsequently re-ducing its maintenance costs.
There are current standards that serve as a guide for implementing this methodology, defining con-cepts related to the RCM and indicating the best course of action. There are two standards to note: the norm IEC 60300-3-11: Application guide – Re-liability Centered Maintenance and the worldwide standard on RCM, SAE JA1012: SAE Interna-tional. A Guide to the Reliability-Centered Mainte-nance (RCM) Standard.
- HOW TO APPLY THE RCM IN A COMPANY
The first step towards implementing the RCM is to plan and choose the assets that will be covered by this methodology and define the personnel re-sponsible for implementation. The choice of as-sets for this project must be based on the im-portance of the production process, maintenance history and experience using these assets.
The implementation of this methodology can be assisted by the help of the Failure Mode and Ef-fect Analysis (FMEA) tool. This tool assesses risk management with the aim of reducing flaws de-tected in the processes or systems by identifying them. Analyze possible failures, the symptoms tha are detected (failure modes) and the associated consequences (effects) for all predefined assets so that the system can be improved to avoid fail-ures.
When targeting the detection of faults, another tool can be utilized, namely Risk Priority Number (RPN).
This tool follows a system whereby the a number corresponds to the level of attention that should be given to any fault. To calculate this value, we analyzed three variables that will be rated between 1 and 10 (10 being the worst-case scenario). This number signifies the severity of the fault, probability of occurrence and ease of detec-tion.
Finally, the most appropriate maintenance activity for each asset is chosen, taking into account the failures associated to the asset.
Where the failure is more frequent and the asset is essential for the production process, the mainte-nance of this piece of equipment must be mainly preventive, whereas an asset that has infrequent faults and is not so important to the productive process will mostly require corrective mainte-nance, taking into account the cost of each repair. I would like to draw your attention to the fact that sometimes corrective or preventive maintenance may not be the only solution for frequent failures. For certain cases, it is necessary to change sup-plier, layout or operator to analyze the situation.
Where failure is frequent and the equipment is not important for the process, or where the failure is infrequent and the asset is important for the pro-duction process, the maintenance department must carefully choose the assets that require more attention than others, factoring in the pro-duction process and the resources available to the maintenance team.
In order to for an RCM implementation to suit the organization’s structure and activities, it is imper-ative that the seven basic questions of this meth-odology are answered. The relationship with the asset or system should be considered and planned for in advance, with the role it plays in the company’s production process being noted.
1 – How the standard roles and performance levels of an asset are identified?
Outline the primary functions of the asset that per-tain to customer satisfaction, alongside the likeli-hood of these functions to be fulfilled.
2 – How the asset fails to perform its function?
Identify the failure modes of the asset. The failure mode can be seen as the chaining of situations that can cause the asset to fail.
3 – How the causes of asset failure are identi-fied?
Determine the causes that can lead to asset fail-ure.
4 – What the effects of asset failure are?
Identify how the failure compromises the quality and costs associated with the final product.
5 – Identify the consequences of asset failure modes?
How do failures affect the asset while in operation, the system that comprises the asset, the organi-zation as a whole, security and the environment.
6 – What is the best preventive maintenance plan to avoid asset failure?
Define the maintenance tasks that best suit the asset and the periodicity within which they will be performed with the aim of maximizing efficiency.
7 – What is the procedure to follow when the preventive maintenance solution fails?
Review the preventive maintenance plan again and make the necessary changes.
Once the previous step is finished, the mainte-nance plan is structured based on the information resulting from the analysis made previously.
- RCM POST-IMPLEMENTATION ANALYSIS
After implementation, the adequacy of the plan in practice should be analyzed as soon as a gap or error in the plan is identified.
There are useful indicators that can be used to check post-implementation progress, one of which is MTBF (Mean Time Between Failure). This indicator tells us the average time between two failures, and controlling this variable is recom-mended as the higher the value of this indicator, the more the available the asset is, and therefore, the strategy in question can be rendered ade-quate.
Another recommended indicator is MTTR (Mean Time To Repair). This indicator refers to the average repair time, and the lower this value is, the less downtime the asset will have in the pro-cess. These two indicators are the main ones per-taining to asset availability.
Finally, the main indicator is the availability of the asset. According to the EN 13306 standard, this indicator refers to the ability of an asset to fulfill a required function under certain conditions at a given time or a certain period of time.
- BENEFITS OF RCM IMPLEMENTATION
After implementing the RCM methodology, organizations tend to increase their competitiveness and vision in their respective market. Some of the expected benefits associated with the implementation of the RCM strategy are highlighted, such as the reduction of corrective maintenance activities; reducing the costs of maintenance programs; the increase in the availability of assets; and the increase in longevity of assets. - STATISTICAL DATA
The data below outlines the results of a survey study involving the opinions of approximately 100 maintenance-related professionals, such as service providers, industrial professionals, and public administrators.
• 69% have identified failure modes for their equipment/systems.
• 90% say that identifying failure modes pre-vents failures.
• 57% believe that they have a standard procedure when they identify the failure mode.
All respondents claim to have a preventive maintenance plan, with 43% constructing the maintenance plan based on information from the manufacturer; 31% based on the asset’s history; 15% on experience; and 11% on other methods. The graph below shows this data.
As for the financial impact caused by the unavailability of assets, 36% of respondents claim that the impact is ‘very high’, 29% claim it was a ‘high impact’, 24% answered with ‘low’ and 12% are unable to determine the impact caused by the unavailability. The graph below shows this data.
86% noted that they can detect when a piece of equipment is no longer reliable, of which 39% identify this based on experience, 20% on analy-sis, 27% on a deep analysis that is comple-mented with experience, and finally 14% of re-spondents said they cannot recognize when equipment is no longer reliable. The graph below shows this data.
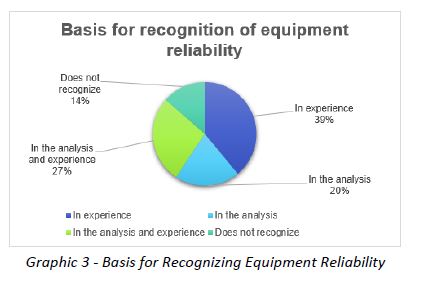
- FINAL CONSIDERATIONS
The considerations below are the result of a study carried out by the authors where, in addition to the related literature, a survey was carried out on roughly 100 professionals, which produced the following results:
• Nowadays, more organizations are looking for new management techniques to remain competitive in their respective markets.
• RCM implementation tends to optimize an or-ganization’s maintenance strategies.
• The implementation of an RCM tends to boost the company’s productivity.
• The application of an RCM involves identify-ing strategic maneuvers that, when executed well, seek to reduce the probability of equip-ment failure and increase reliability and avail-ability.
• The implementation of the RCM must be rec-ommended with the help of the Failure and Effect Modes Analysis tool – FMEA.
Organizations increase their competitiveness and vision in the market in which they oper-ate when the implementation of an RCM methodology is successful.
BIBLIOGRAPHIC REFERENCES
[1] Cabral, J. P. S. (2013). Gestão da Manutenção de Equipamentos, Instalações e Edifícios. Lisboa: Lidel
[2] SAE JA1011 Evaluation Criteria for Reliability-Centered Maintenance (RCM) Processes, Society of Automotive Engineers, 1998.
[3] MOUBRAY, J. Reliability-centered maintenance: second edition. 2ª. ed. New York: Industrial Press Inc., 1997.
[4] NOWLAN, F. S. & HEAP, H. F. Reliability-Cen-tered Maintenance. Technical Report AD/A066-579, National Technical Information Service, US Departament of Commerce, Virginia, 1978.
[5] SANTOS, Thiago Alan Dutra dos. Aplicação da Manutenção Centrada em Confiabilidade em Aciaria de Usina Siderúrgica. Trabalho de Conclusão de Curso (MBA Especialização em Engenharia de Manutenção) – Universidade Federal do Rio de Janeiro, Rio de Janeiro, 2011. [Consult. 28.06.2019] Available in http://hdl.handle.net/10071/18286.